
Probabilistic studies based on 3D models with random ω are carried out to evaluate the effect of uncertainty in ω on the accuracy of GNA with the extended beam-column flexural stiffness reduction factor. The proposed model to predict the effective moment of inertia for R/C beam with GFRP bars was developed empirically, based on Branson’s equation to have better accuracy and a familiar approach to a structural. It is found that GNA with the extended flexural stiffness reduction factor (using beam element) generally achieves the accuracy of GMNIA (using shell element). The authors carried out experimental and analytical research to evaluate the flexural capacity and the moment-deflection relationship of concrete beams reinforced with GFRP bars. For in-plane stainless steel elements with non-compact and slender sections, results determined by the extended flexural stiffness reduction factor coupled with Geometrically Nonlinear Analysis (GNA) are verified against those determined by Geometrically and Materially Nonlinear Analysis with Imperfections (GMNIA). The rectangular beam forms the web of the T-section. The flange of a T-section is formed by the effective width of the slab, as defined in Section 8.10 of ACI 318-05, and also illustrated in Flexure 6. The resulting one-way structural system has a T-section. ρ, determined by the Direct Analysis Method, depending on cross-section slenderness, is adopted. participating in flexural resistance of the beams. Local buckling effects and the influence of ω are accounted for by means of reducing the gross section resistance using a strength reduction factor ρ. I=Moment of inertia about the neutral axis, m 4Ģ0.In this paper, flexural stiffness reduction factor formulations, applicable to stainless steel members with compact cold-formed square and rectangular hollow section (SHS and RHS), are extended to account for local buckling effects and initial localized imperfection (ω). Y=Vertical distance away from neutral axis, It can be concluded therefore that the value of the bending stress will vary linearly with distance from the neutral axis.Ĭalculating the maximum bending stress is crucial for determining the adequacy of beams, rafters, joists, etc. In this paper, flexural stiffness reduction factor formulations, applicable to stainless steel members with compact cold-formed square and rectangular hollow section (SHS and RHS), are extended to account for local buckling effects and initial localized imperfection (). The bottom fibers of the beam undergo a normal tensile stress. The stress at the horizontal plane of the neutral axis is zero.

Increasing in flexural stiffness, leads to increase in pile stiffness, but near ultimate resistance, if flexural stiffness would be high, gradient of stiffness reduction would be high too. EI) Steps 2 to 4 are repeated until convergence or the iteration limit is reached.When a beam experiences load like that shown in figure 20.1 on the top fibers of the beam undergo a normal compressive stress. stiffness, the pile failure capacity would not change, albeit, the ultimate capacity is affected a little. Flexure stiffness of selected members is set to (0.80× b Bending stress is a more specific type of normal stress. When a member is being loaded similar to that in figure 20.1 flexure stress (or bending stress) will result. It is measured in terms of stress, here given the symbol σ.
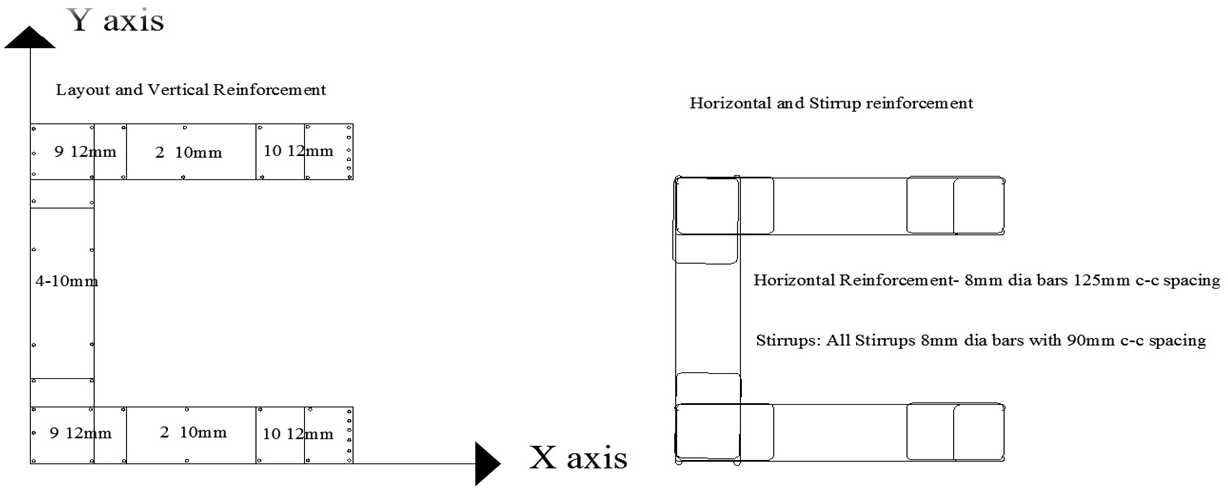
The flexural strength represents the highest stress experienced within the material at its moment of rupture. In accordance with current design standards, the ultimate limit state for this method is the formation of first plastic hinge, and the adequacy of the method is confirmed through member-based resistance checks.The focus of the thesis is the development of flexural stiffness reduction factor formulation for the in-plane stability design of. The transverse bending test is most frequently employed, in which a rod specimen having either a circular or rectangular cross-section is bent until fracture using a three point flexural test technique. Flexural strength, also known as modulus of rupture, bend strength, or fracture strength a mechanical parameter for brittle material, is defined as a material's ability to resist deformation under load.
